Die Maschine ist so groß wie ein Schulbus und kostet 120 Millionen Euro. Sie besteht aus mehr als 500.000 Einzelteilen. Das Innere der Maschine erinnert an Szenen aus Science-Fiction-Filmen: Ein Hochleistungslaser beschießt zweimal in rascher Folge Zinntropfen, erst, um sie zu verformen, dann, um sie in Plasma zu verwandeln. Dies geschieht 50.000-mal pro Sekunde. Das Plasma strahlt UV-Licht ab. Hochpräzise Rundspiegel sammeln dieses Licht ein, um damit eine Maske – eine Art Schablone – zu beleuchten und sie auf Fotomaterial zu bannen. Dies geschieht mit etwa 100 Schablonen, sodass Schicht für Schicht ein komplexes dreidimensionales Gebilde entsteht – ein Wafer, die Grundplatte heutiger Mikrochips. Die Entwicklung der extrem ultravioletten Lithografie (EUV-Lithografie) ermöglichte dabei eine Grenzüberschreitung: Mit ihr passen mehr Transistoren auf die ohnehin winzigen Chips – und somit auch mehr Rechenleistung.
Impact of Science
EUV-Lithografie – neues Licht für das digitale Zeitalter
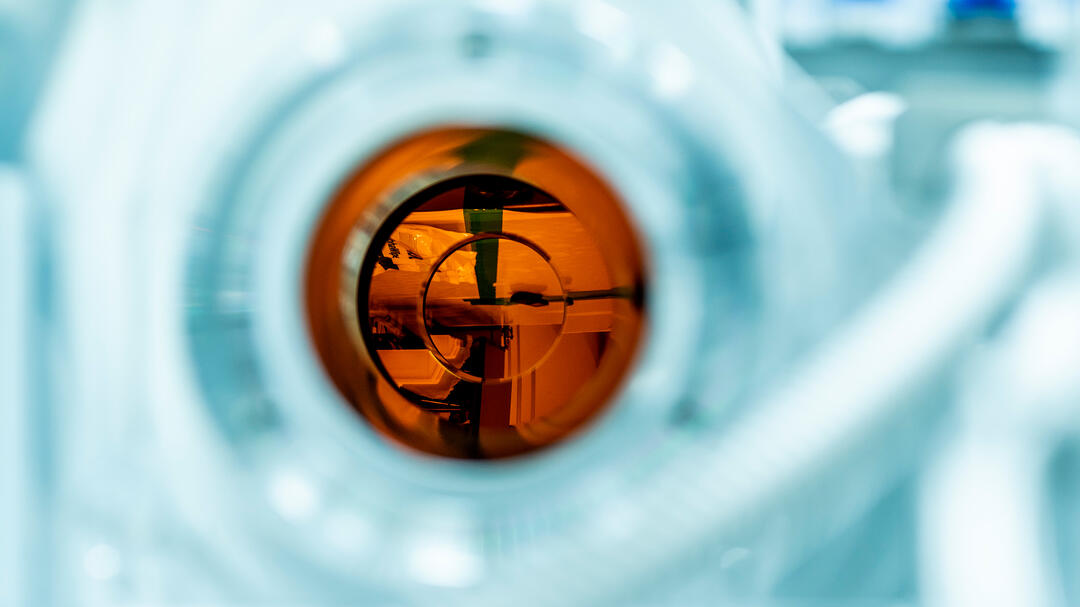
Der Deutsche Zukunftspreis 2020 geht an das Projekt EUV-Lithografie, einer einzigartigen Kooperation von Firmen und Forschern. Die Technologie ermöglicht eine neue Generation von Chips für mobile Geräte, Smart-Home-Anwendungen oder autonomes Fahren.
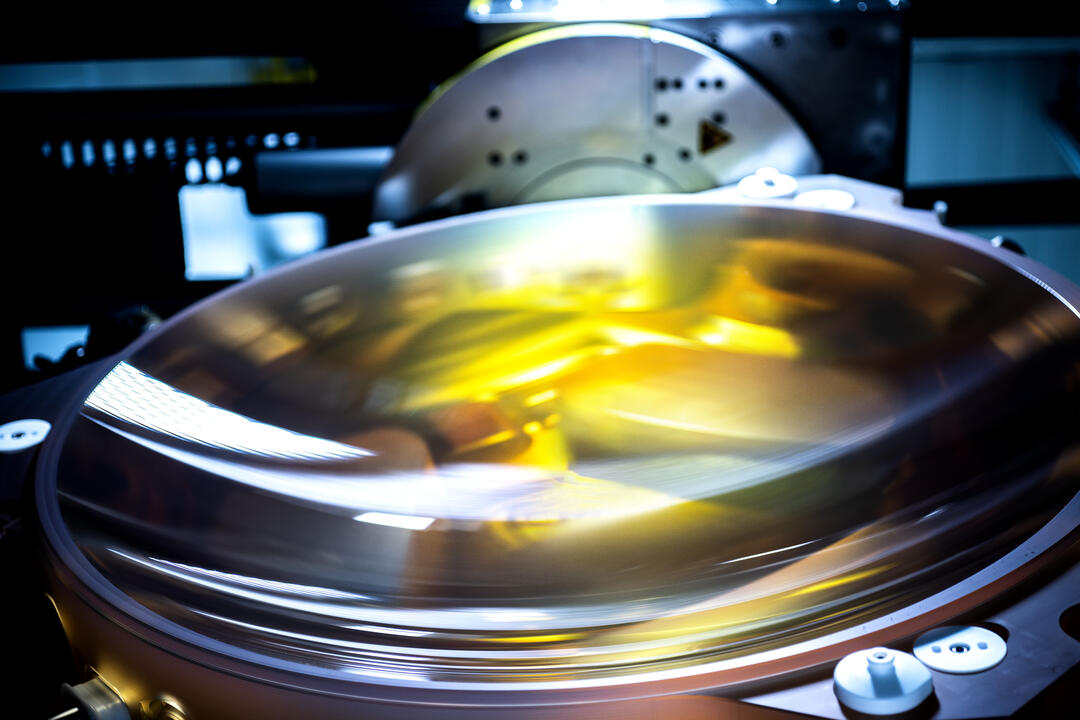
Kein Mikrochip ohne die Erfindung von Zeiss, Trumpf und Fraunhofer
Jeder kennt Marken wie Apple oder Intel. Es ist auch kein Geheimnis, dass asiatische Firmen in der Chipproduktion führend sind. Aber nur wenige wissen, dass die gesamte Branche auf eine Innovation aus Europa angewiesen ist, um ihre Technik voranzutreiben. Denn nur die niederländische Firma ASML mit ihren deutschen Partnern Carl Zeiss und Trumpf sowie Forschungspartnern wie dem Fraunhofer-Institut für Angewandte Optik und Feinmechanik IOF sind derzeit dazu in der Lage, die hochleistungsfähige, präzise Maschine für die EUV-Lithografie herzustellen. 80 Prozent aller Chiphersteller sind Kunden von ASML. Die EUV-Lithografie ist das Resultat einer jahrzehntelangen disziplinen-, länder- und firmenübergreifenden Zusammenarbeit, die nun mit dem Deutschen Zukunftspreis (siehe Kasten) ausgezeichnet wurde. Sie ist eine Voraussetzung für Innovationen, sei es für das Smart Home, die Smart Factory, für Robotik oder mobile Geräte.
„Wir sehen uns alle als ein großes Team.“
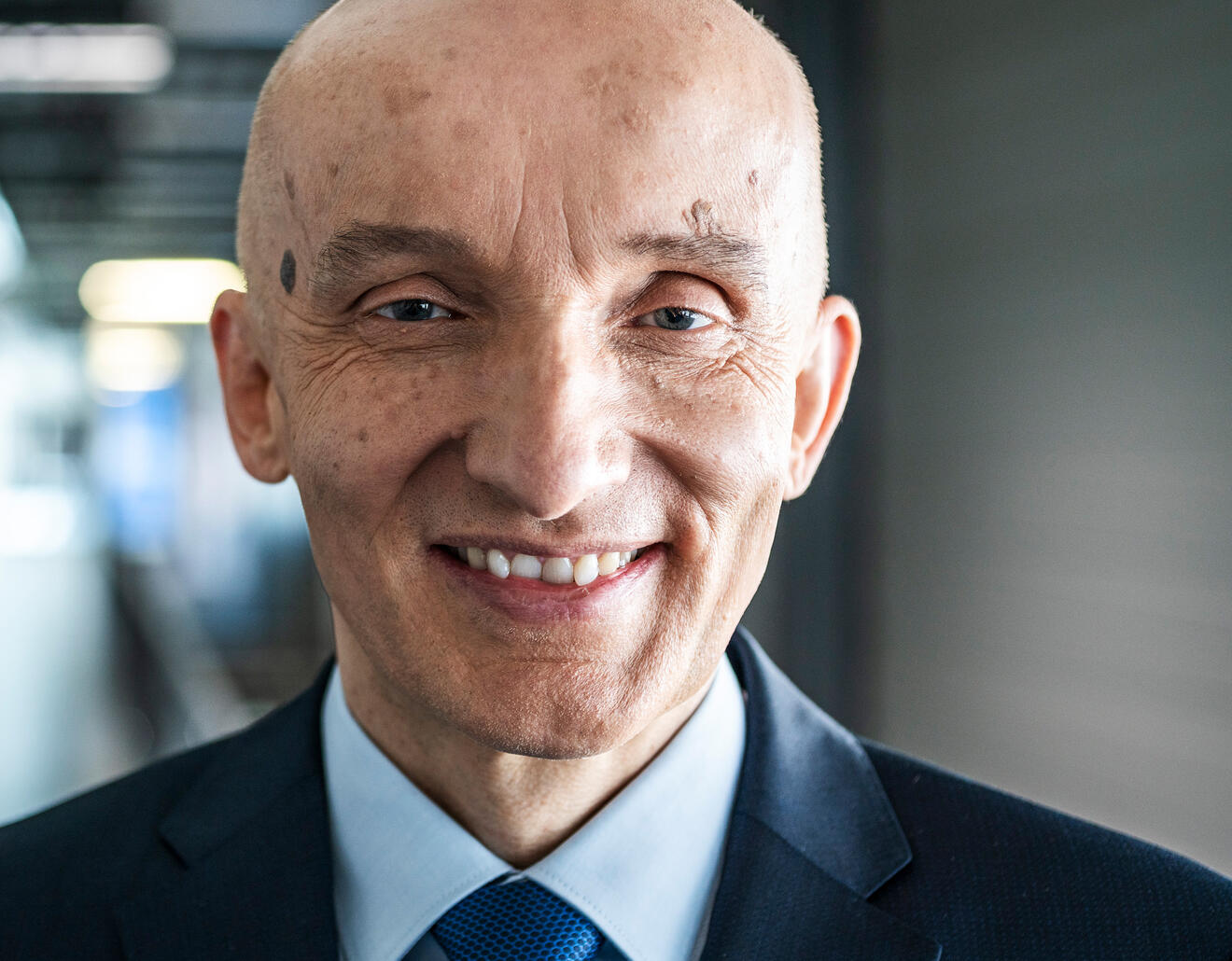
Erfolgsrezept: Vertrauen und Team-Arbeit
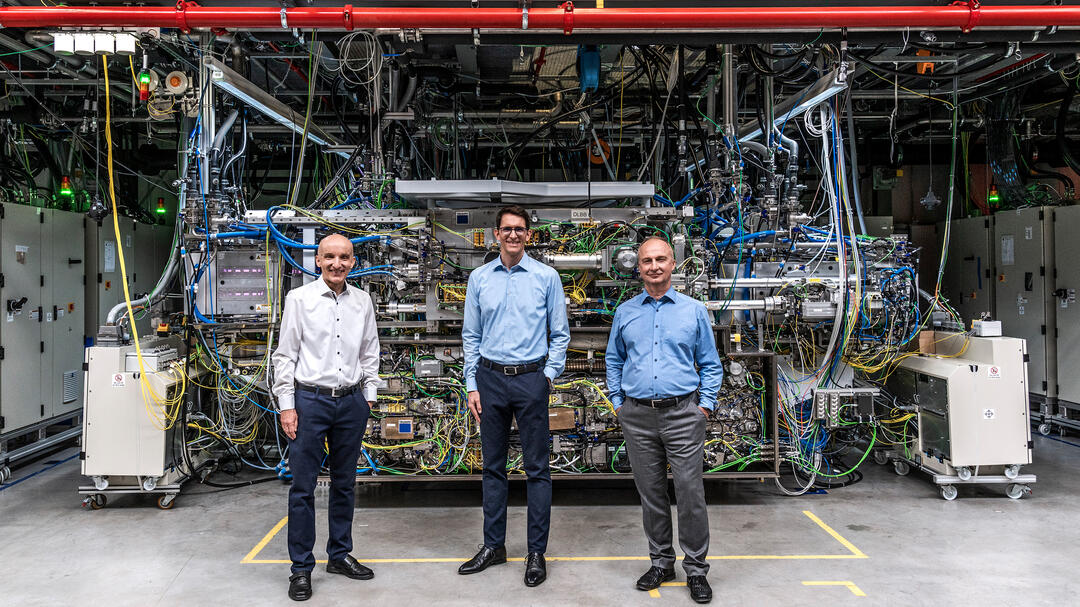
Inzwischen hat ASML mehr als 100 Systeme verkauft. Sie müssen mit vier Boeing-Flugzeugen zum Kunden transportiert werden. Einmal installiert, laufen sie stabil. Künftig soll das System noch kleinere Strukturen hinbekommen – und höhere Durchsätze. Letzteres gelingt durch die Weiterentwicklung des Lasers. Ersteres hängt von zwei Faktoren aus der Optik ab: Zum einen erhoffen sich die Entwickler, geringere Wellenlängen beim UV-Licht nutzen zu können, zum anderen möchten sie die Öffnungswinkel der Optik vergrößern – die sogenannte numerische Apertur. In beiden Fällen wäre eine bessere Auflösung möglich, was bedeutet, dass noch mehr Strukturen auf dem Wafer untergebracht werden können.
Die Unternehmen vertrauen sich gegenseitig. Ihre Innovationen sind durch mehrere Tausend Patente abgesichert. ASML-Vorstand Christophe Fouquet sagte kürzlich: „Wir können nicht ohne Zeiss und Trumpf, aber unsere Partner können auch nicht ohne uns.“ Die Ingenieure arbeiten dabei längst über Firmengrenzen hinweg eng zusammen – insgesamt sind mehr als 2.000 Menschen involviert, darunter auch die Netzwerke jeder der drei Partner. „Kommunikation ist dabei immens wichtig“, sagt Kürz. „Wir haben nahezu täglich Telefonkonferenzen und in Nicht-Corona-Zeiten auch viele Besuche vor Ort.“ Die können auch länger ausfallen. Kösters arbeitete etwa drei Monate direkt bei ASML. „Wir sehen uns alle als ein großes Team“, sagt er. Dabei motiviere man sich auch firmenübergreifend, schließlich möchte keiner den Fortschritt aufhalten. Kürz sagt: „Der Erfolg der EUV-Lithografie ist zweifelsohne das Ergebnis einer gelungenen Zusammenarbeit.“
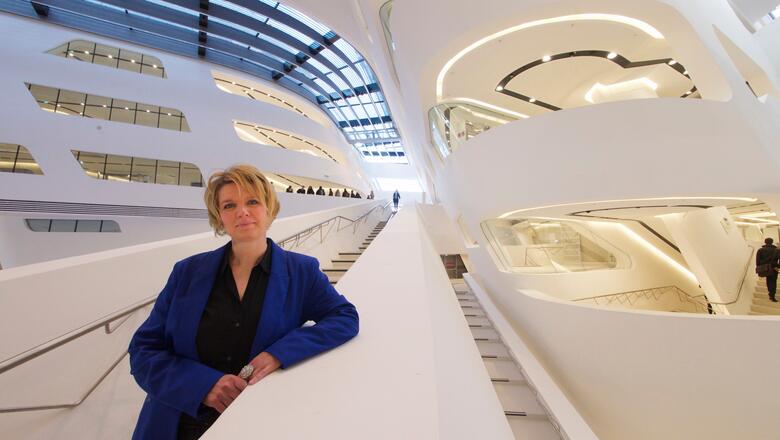